This week’s maker is 4th year student in the UCSF School of Medicine, Gavin Sowa. We caught up with Gavin during a break from his research to see what he is making.
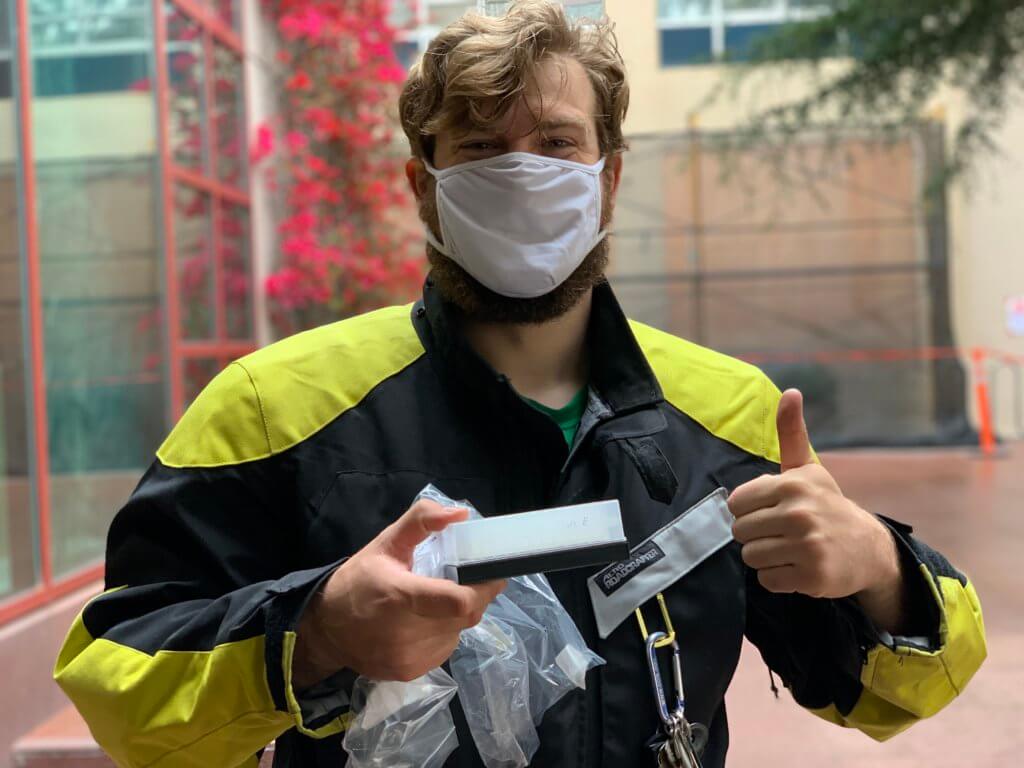
Q: What did you make?
I wanted to make an adapter that would let me spin down filter plates so liquid would be spun off of the top lid but any liquid that came through the filter plate would be caught by the adapter.
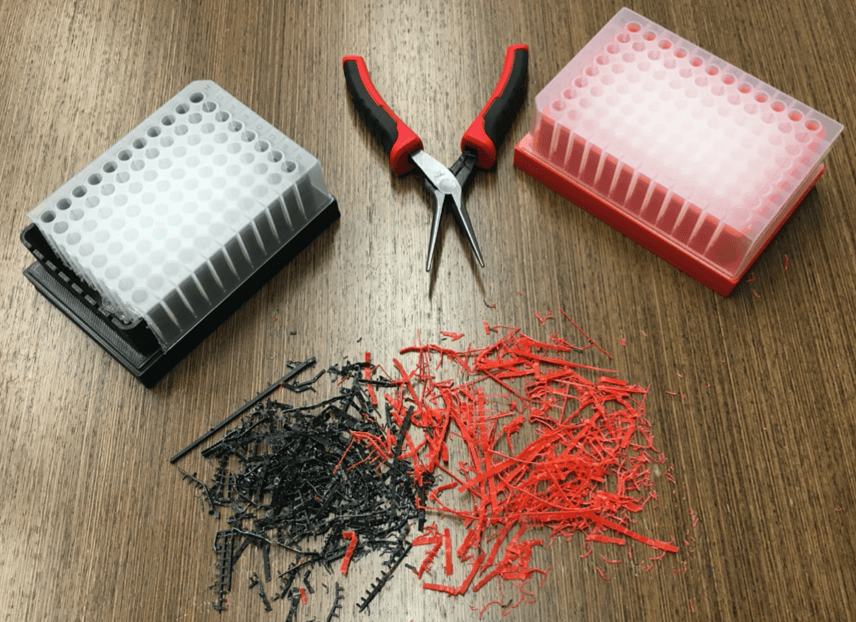
Q: Why did you want to make it?
I can’t really get into the details of the method because it isn’t published yet, but there is a step in the procedure where you need to spin down filter plates. There is a small amount of leakage, but even a little leakage can really make a mess in a centrifuge! Previously, people using the protocol were taping the bottom of the plates, but this was time consuming for me and there was still leakage. I thought this would be a good opportunity to make a reusable plate adapter to solve all of the above problems.
Q: What was your process?
I recently attended the Fusion 360 workshop offered by the UCSF Makers Lab. I’m mostly self-taught, so it was a great opportunity to pick up a few new tips and tricks. One of the ideas I used from the workshop was emailing the company that made the filter plates to get the engineering drawings that I could import as a canvas. This was a great place to start, but I found that I needed to go back and adjust my tolerances after taking measurements with a set of calipers. I bought a really cheap pair off of eBay like a year ago, and they’re really worth their weight in gold. Then you can go back into the sketches and make adjustments, print the part and make further refinements as needed. One thing that wasn’t on the engineering drawings was the support structure underneath the plate, so that required big changes to my initial design.
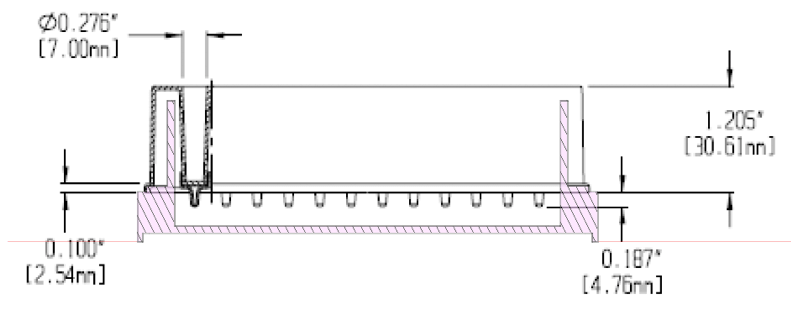
Q: What was the hardest part of the process?
Fusion Deposition Modeling (FDM) is great for prototyping parts, but is inherently crummy at holding liquids. Initially I tried priming/painting the holders but they still leaked. I got much better results from printing in ABS, acetone vapor smoothing, and then coating in an epoxy (like XTC-3D). I see a lot of really great looking smoothed parts on the internet, and that’s a reminder that there’s still a lot of room to refine the process.
Q: What was your favorite part of the process?
Collaborating with my friends and the Makers Lab! Jamin Liu and Sabrina Mann in the DeRisi Lab are super talented, and had a lot of really great design feedback. Also, Eric Lam at the KAVLI-PBBR Fabrication and Design Center has been really generous with his time as we are transitioning to the production phase.
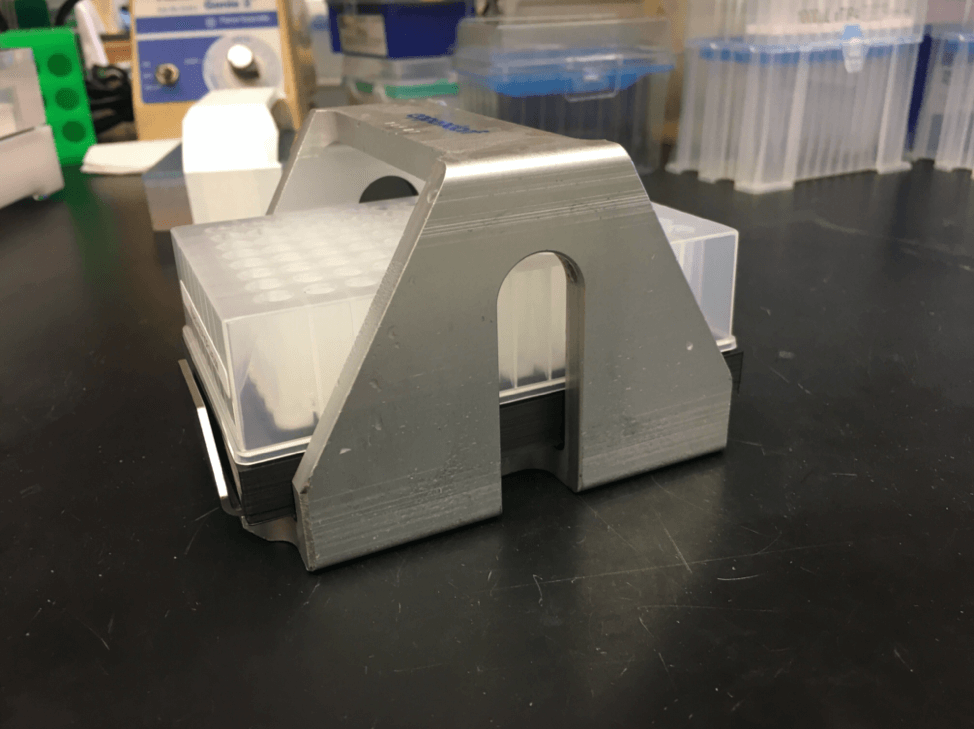
Q: Why did you make it instead of buying it?
If this was already on the market I would have bought it in a heartbeat! It would have been a lot easier and cheaper (but a little less fun) to buy this off the shelf. Maybe Thermo Fischer will buy my design so I can graduate debt free? Lol. In all seriousness, once we are happy with a final design and the paper is published I plan on putting the design on the NIH 3D Print Exchange. I’m a big believer in making things open source.
Q: How did this help make you a better student/researcher?
It’s very difficult to start out making super complex assemblies with lots of moving parts as your first project. My first forays into 3d printing were just printing designs I found on Thingiverse. When that turned out fine I tried my hand at designing simple objects such as a label for my stethoscope, a hook for my headphones, etc. So, it’s kind of a natural progression. I think the Makers Lab lowers the activation energy of getting in practice and then trying risky projects that aren’t guaranteed to work. Every student printing a name tag or a T-Rex skeleton could go on to design the next cool implantable device. It’s a neat skill to have, but the trick is to start developing your skills before you actually need them.
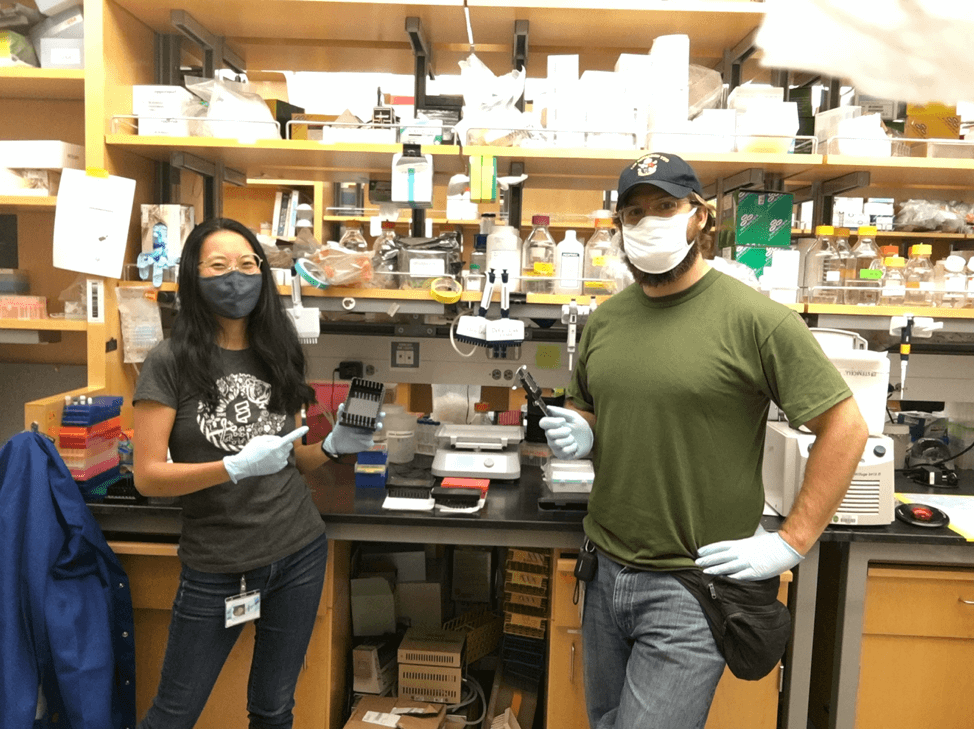
Q: What do you want to make next?
I want to make a booby trap on my bench so people will stop borrowing my phone charger! Just kidding. Anyhow, I think it’s really cool when people value your work and start to adopt your methods. I’ve had enough labmates ask for their own set of plate holders now that we’re starting to move away from the prototyping phase, and into the production phase. We’ve started looking into more durable materials, and different manufacturing techniques. This is all pretty new territory for me, so I’m really excited to see how this plays out. I also need to add the lab logo to the plates. In the near future I want to try making some bench-top equipment as an excuse to get better at multi-component assemblies, micro-controllers, etc.